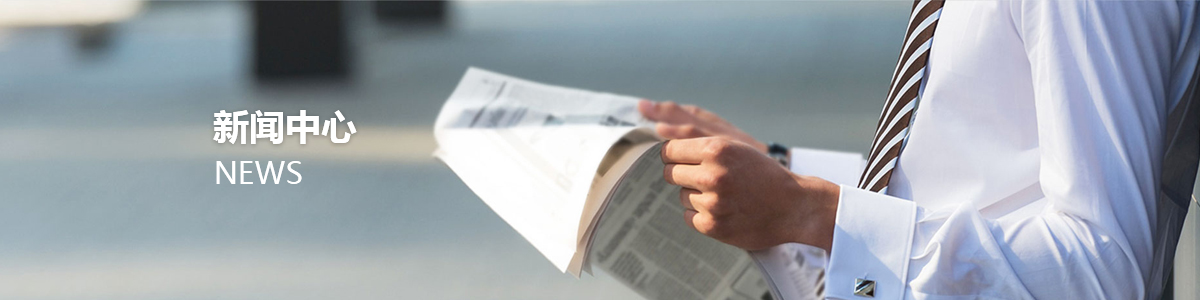
一、FMEA能解決哪些問題?
FMEA,全稱為 Failure Mode and Effects Analysis,即失效模式和影響分析,被用于循序漸進地識別和分析流程或產(chǎn)品可能失敗的所有可能方式,并設計策略以優(yōu)先發(fā)現(xiàn)并最大化降低風險。
FMEA主要解決以下4大問題:
■ 可能發(fā)生什么問題?
■ 失敗的原因是什么?
■ 失敗的可能性是多少?
■ 失敗帶來哪些后果?
由上可知,F(xiàn)MEA能幫助設計人員在起始階段便創(chuàng)建高質量和可靠的流程,并通過評估過程風險,以改進系統(tǒng)并降低故障的可能性和影響,從而避免高昂的損失。
二、FMEA適用于哪些情況?
■ 對新的設計或流程的分析;
■ 對現(xiàn)有產(chǎn)品設計或流程的修改;
■ 在新環(huán)境或應用程序中使用設計或流程。
提示:在服務、產(chǎn)品或流程的完整生命周期中定期開展FMEA 分析,可確保一切順利進行,是值得推薦的做法。
三、FMEA采用什么標準分析問題?
■ 影響的嚴重程度;
■ 發(fā)生的可能性;
■ 預先發(fā)現(xiàn)問題的概率(故障被檢測到的難度)。
提示:以上各項標準在1-10的范圍內評分,然后一并用于計算風險優(yōu)先級(RPN)。RPN可幫助識別、確定需優(yōu)先關注的問題,最高級別RPN應被立即關注并制定行動計劃以降低相關風險。
四、FMEA的開展流程是什么?
1. 確定分析對象
確定需要被評估的產(chǎn)品或流程。
FMEA屬于綜合性分析,專注于范圍相對較窄的特定過程。
針對復雜流程,可考慮將項目分解為較小部分并開展多次FMEA分析。
2. 組建分析團隊
組建跨職能團隊以實現(xiàn)徹底的分析,成員應當直接參與正在分析的過程。成員可能來自設計、制造、維護、銷售或客戶服務,包括非管理人員,以清晰了解實際的過程和挑戰(zhàn)。
3. 審查流程
查看當前過程并確定各組成部分和功能,應當具體考慮該過程目的、客戶期望。
建議:使用工具繪制流程圖(見下圖),以幫助了解當前過程并使?jié)撛陲L險區(qū)域可視化??稍诰€運行的流程圖工具,使得團隊協(xié)作更容易,并確保不遺漏任何組件。
4. 識別故障模式
集思廣益地以各種方式分解流程。故障模式需要分析的問題有:存在哪些風險?各組件如何失效或出現(xiàn)故障?
重要提示:某一組件故障可能會導致其他組件的另一個故障。
5. 羅列潛在故障模式的后果和原因
羅列全部潛在故障模式后詳細檢查各種模式,并確定對系統(tǒng)\流程\客戶或組織產(chǎn)生的所有后果。
換言之,對各種故障模式需詢問的問題有:
■ 當此功能失敗時將出現(xiàn)哪些情況?
■ 該故障如何影響客戶?
隨后,考慮每次失敗的根本原因,并在FMEA圖上寫明原因。
↑失效模式和影響分析案例
6. 對嚴重程度的評分
根據(jù)問題嚴重程度計算分值,1分代表微不足道,10分代表災難性。分值被加入FMEA圖表。
7. 對發(fā)生概率的評分
對每種故障模式的發(fā)生次數(shù)或概率進行評分。
分值介于1到10之間,1表示可能性最小,10表示必然發(fā)生,分值需被加入FMEA圖表。
8. 對可檢測程度的排名
即:故障發(fā)生前(或客戶注意到故障前)檢測出故障并采取行動的可能性。
需首先確定:當前已采取哪些控制措施,以防止故障發(fā)生或防止問題影響到客戶?
了解控制措施后,可對故障被檢測到的可能性進行排名。以1-10的等級進行概率排名,1表示確定檢測到故障,10表示確定不會檢測到故障。
9. 計算RPN
在FMEA表中對每個標準進行評分并列出后,將以上3項評分相乘以計算風險優(yōu)先級RPN:嚴重程度x發(fā)生次數(shù)x可檢測程度=RPN。
RPN有助于確定最緊急故障的優(yōu)先級,以便制定戰(zhàn)略行動計劃。
10. 根據(jù)風險優(yōu)先級制定行動計劃
對故障模式進行排名后,可快速評估出需采取糾正措施的流程區(qū)域。
以上可能意味著對流程或產(chǎn)品設計進行更改,或調整現(xiàn)有的控制措施以降低風險。
具體行動計劃應注重以下目標:
■ 盡可能完全消除過程中的故障模式
■ 最小化嚴重性并減少故障模式的發(fā)生
■ 改進故障模式檢測(即改進控制措施)
提示:實施改進措施后,需注意結果并重新計算RPN。
五、觀 點 總 結
對于性能和可靠性嚴重影響用戶安全的醫(yī)療器械,F(xiàn)MEA是極具價值且十分直觀的分析工具。
因此,制造商應考慮將FMEA作為風險管理流程的關鍵組成。
此外,醫(yī)療器械風險管理若想取得實質性進展,應消除生產(chǎn)企業(yè)對風險管理的模糊認識,增強責任意識,發(fā)揮對其受益者的作用。
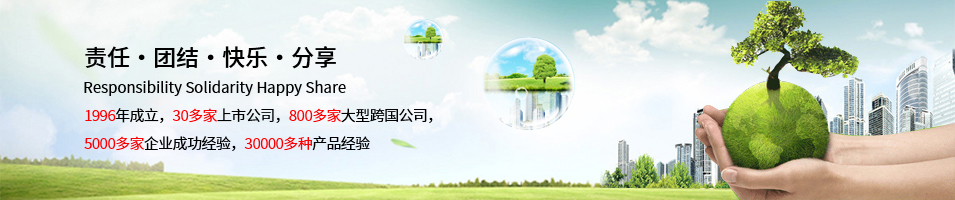